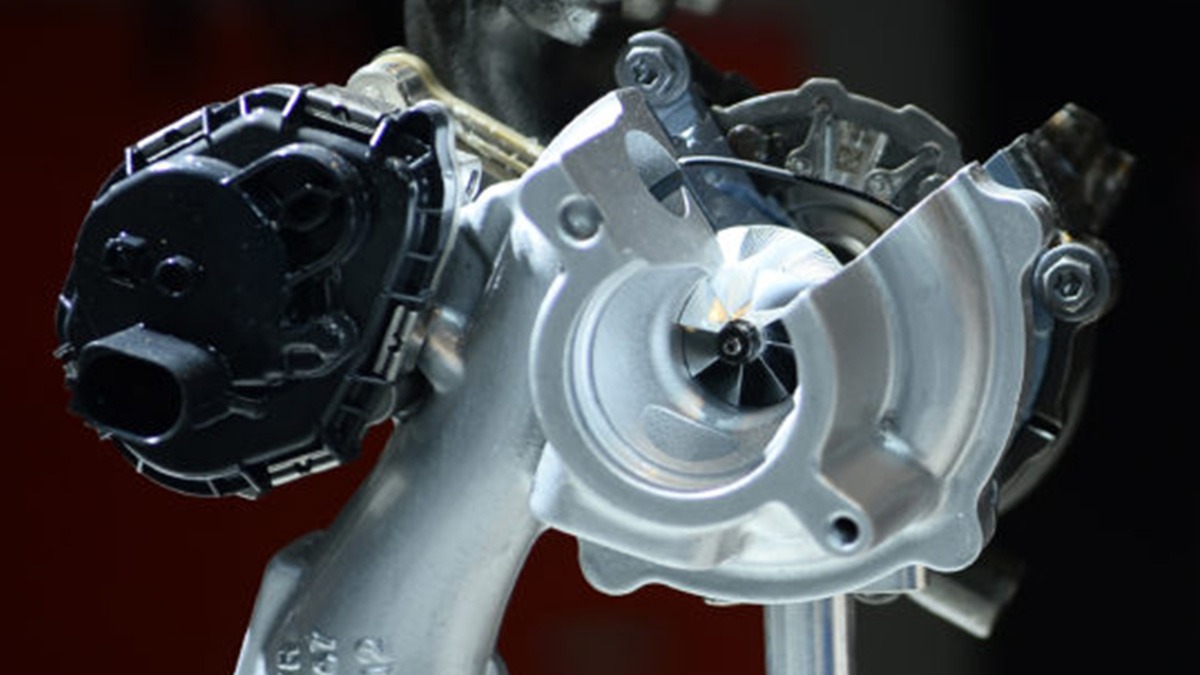
With this helpful guide from our friends at Garrett, we will show you some of the types of turbocharger that are fitted on current vehicles.
Micro Turbos

Garrett’s micro turbo technology is ideally matched to the needs of the small car segment in emerging markets, supporting the unique requirements of two and three-cylinder diesel engines and gasoline engines less than 1L by improving driveability and fuel economy.
In 2010, Garrett launched its smallest-ever wastegate turbo for the world’s first 2-cylinder turbocharged diesel engine in India. Compared to a non-turbo equivalent, the Garrett boosted 2-cylinder diesel engine offers a remarkable 25 percent improvement in power along with significant fuel efficiency gains and lower emissions.
Small Wastegate Turbos
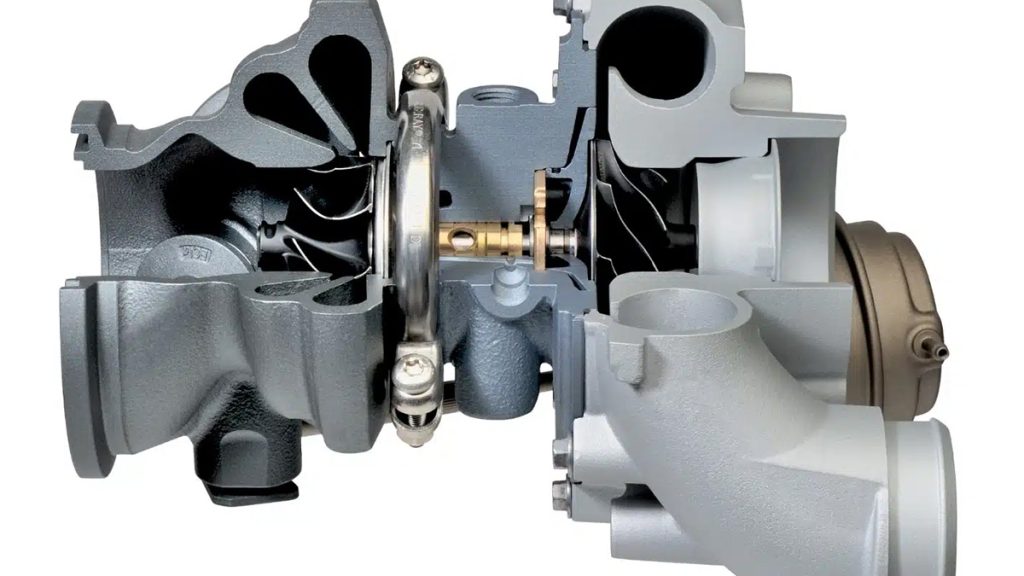
Small wastegate turbos are being widely used today on various engine platforms globally for their proven reliability and cost advantage. Compact fixed-geometry turbos will continue to play an important role as their designs continue to evolve to help achieve advances in performance, fuel efficiency, and emissions control.
Wastegate technology for diesel applications first went mainstream in 1978 when Garrett TA03 was the first mass production turbo for diesel engines in Europe. Two years later, the Peugeot 604 set the scene for the rapid penetration of turbo diesel technology as the vehicle gained in popularity. For many people, the 604 became the first experience of just how responsive a “modern” turbo diesel could be.
In recent years, Garrett diesel wastegate turbos have been continuously upgraded to meet the demands of the new era when lower emissions and better fuel efficiency are the norm.
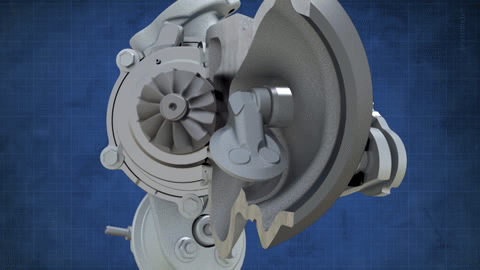
Garrett VNT Turbos
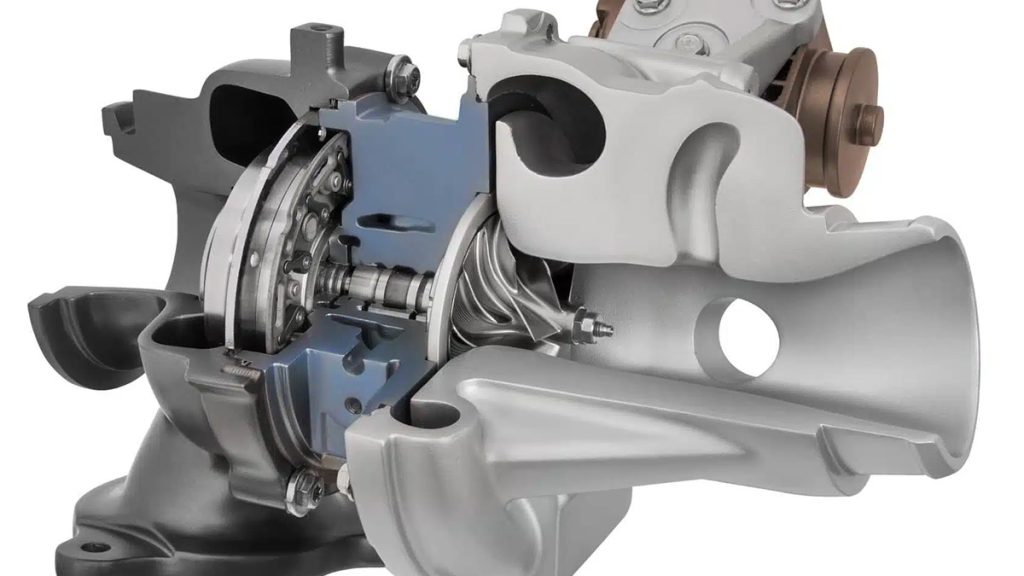
With over 50 million units in the field, Garrett Variable Geometry Turbo (VNT) is a key variable geometry turbo technology for auto manufacturers as they seek to enhance light vehicle driveability, improve fuel efficiency and reduce emissions.
The latest generation VNT delivers benchmark transient response, low-speed efficiency, reliability, weight savings and packaging flexibility.
The current Garrett Variable Geometry (VNT) turbos are upgraded versions of the third generation VNT launched in 2004. The key advance was the ground-breaking way that the variable mechanisms were attached onto the bearing housing through an elastic shroud. This new platform delivered many innovations – a new cartridge design, new cambered vanes, a new generation turbine wheel, improved aerodynamics and better controllability.
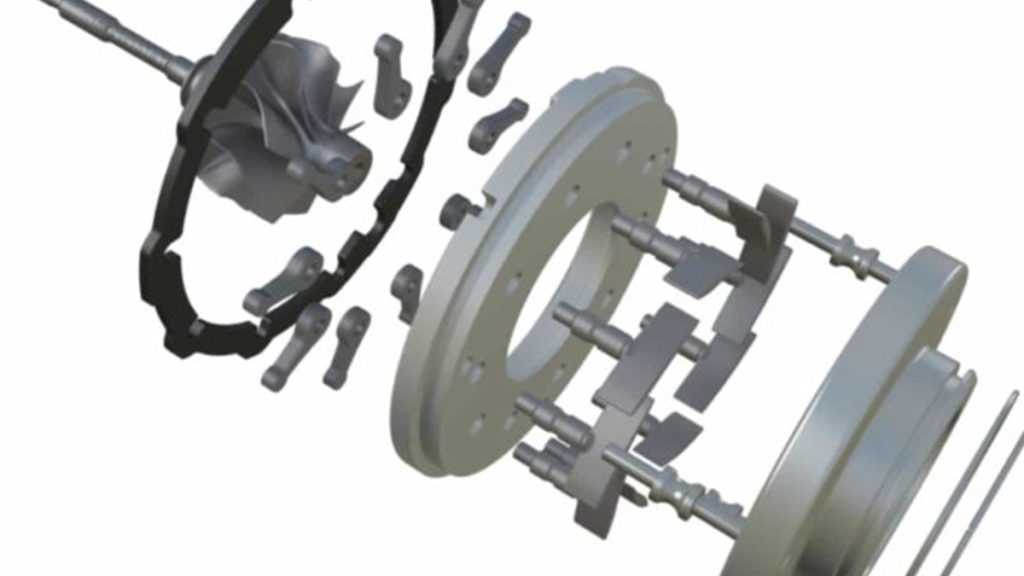
Although launched 20 years ago on the 1.9L Fiat Croma, it was in 1995 that VNT, with a new vane design and improved aerodynamics, really came of age when matched to VW/Audi’s 1.9-litre direct injection diesel engine. Second generation VNT, launched three years later, offered greater controllability through new aerodynamics and electric actuation. Then came the 3rd Generation, launched on the BMW One Series with a new cartridge design, cambered vanes, new turbine wheel and improved aerodynamics… all combining to deliver 130 percent of Generation 2 boost at 90 percent of back pressure.
With its versatility in range and ever-improving capabilities, VNT will remain the leading turbo technology for diesel engines for the foreseeable future. Garrett engineers are working on scale reduction to fit ever-smaller engines as automakers embrace the downsizing agenda, while at the same time, it’s now also a key component in a number of complex two-stage turbocharging systems to deliver superior performance and great fuel efficiency. It’s also increasingly linked to 3 or even 2-cylinder diesel power units. It’s clear that the technology has a great future ahead of it, particularly with ongoing advances in aerodynamics, bearing systems and materials science.
Two Stage Serial Turbos
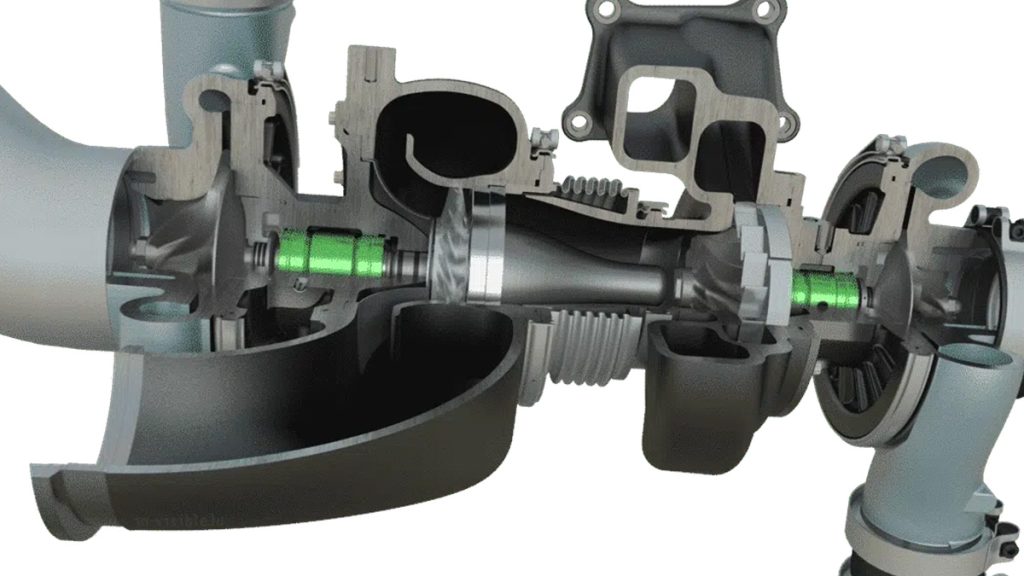
Garrett’s Two Stage Serial sequential system is the ideal turbo architecture for powertrains where ultimate power density and part-load emissions are primary considerations.
This Two Stage configuration is chosen by auto manufacturers either to deliver engine downsizing or to uprate performance.
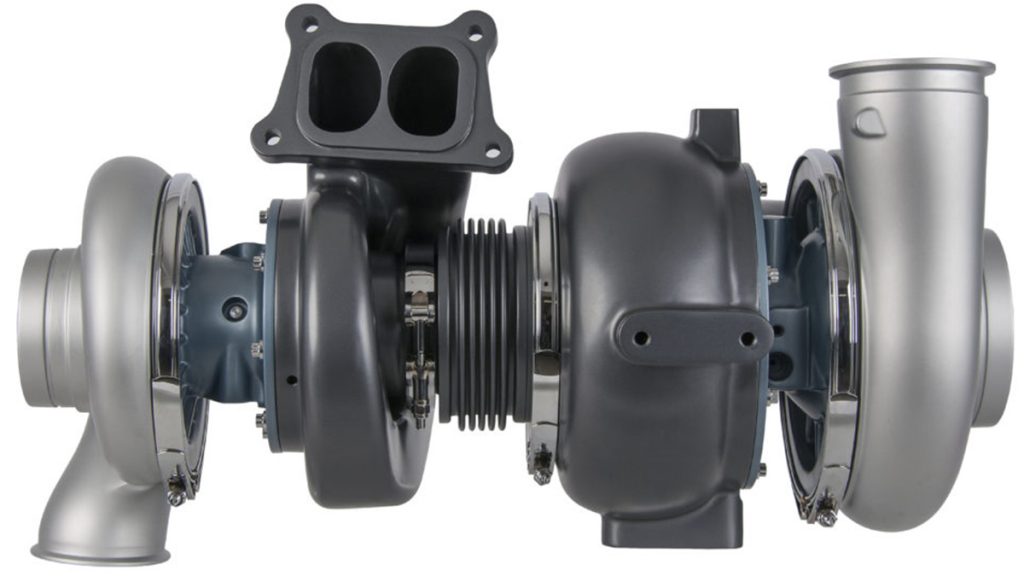
In a Two Stage Serial system, a small high pressure turbo (HP) works together with a larger low pressure turbo (LP). The gas flow between the turbos is controlled using by-pass valves whose operation modes are based on the engine speed. At low-speed – up to about 1500rpm – the two turbos work in full serial mode, with the compressor and turbine by-pass valves closed.
This provides a rapid ramp-up of boost pressure and contributes to enhanced torque and responsiveness. Beyond 1500rpm, the turbos continue to work together, but the turbine by-pass valve progressively channels more exhaust gas to the low pressure turbo until full transition takes place, usually around 2,800rpm. At this speed, both the turbine and compressor by-pass valves are fully open, regulating the gas flow only to the larger LP turbo. The latter thus continues in mono mode, optimizing fuel efficiency and performance at higher engine speeds.
Looking for a new turbo? Click here
Looking to get your turbo repaired? Click here